
How to Dissolve HPMC in Water
Hydroxypropyl methylcellulose, also known as HPMC, is non-ionic cellulose ether derived from refined cotton, a natural polymer material. It is produced through a series of chemical processes. HPMC exists as a white or slightly yellow powder that readily dissolves in water. There are two main types of HPMC: instant type (surface-treated) and hot-dissolving type (non-surface-treated).


Instant-type HPMC rapidly disperses in cold water, initially resulting in a low-viscosity liquid, as the HPMC particles are merely dispersed in water and not truly dissolved. After approximately 2 minutes, the viscosity gradually increases, forming a transparent and viscous colloid.
On the other hand, hot-dissolving type HPMC initially agglomerates in cold water but quickly disperses when introduced to hot water. The viscosity gradually increases as the temperature drops to a specific point, ultimately forming a transparent viscous colloid. The agglomeration in cold water is caused by the cellulose powder on the surface, which reacts with cold water, resulting in an immediate increase in viscosity and the formation of a transparent colloid. Meanwhile, the HPMC inside remains unexposed to water, surrounded by a colloid or powder form, gradually dissolving over time.
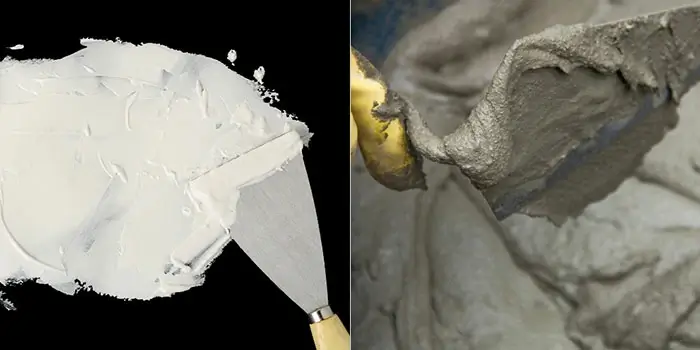
Hydroxypropyl methylcellulose is commonly used as an additive in putty powder, cement mortar, and emulsion-based adhesives. It serves as a water-retaining agent and thickener, enhancing the pumpability of cement mortar.
When added to the putty powder and glue, it acts as a binder, improving spreadability and extending the working time. Let’s take ordinary (hot-dissolving) HPMC as an example to explain the dissolution method of hydroxypropyl methylcellulose.
Materials:
Hydroxypropyl methylcellulose/Water
Beaker/Stirring Rod
Method/Steps:
Hot water dissolution method:
Take 1/5-1/3 of the required amount of hot water (over 85°C) in the beaker, put the HPMC power into the hot water, and stir with a stirring rod until the product is fully dispersed.
Add the remaining hot water (or cold water) and stir until it reaches the appropriate temperature (10°C) for complete dissolution. A magnetic stirrer or mechanical mixer can be used to achieve this.
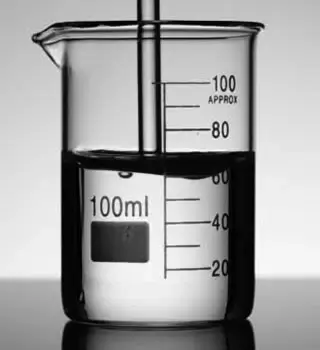
Organic solvent wetting method:
Disperse the HPMC powder into an organic solvent in the beaker or moisten it with an organic solvent.
Add the mixture to cold water or dissolve it well by adding cold water. The organic solvents can be ethanol, ethylene glycol, etc.
Precautions:
- If agglomeration occurs during dissolution, ensure quick and thorough stirring. This may happen if the ordinary HPMC is directly added to cold water.
2. Maintain patience and continuous stirring throughout the process until the HPMC powder is completely dissolved, resulting in a clear and transparent solution.
3. If bubbles form during dissolution, let them settle for 2-12 hours (or as determined by the solution’s consistency) or remove them using vacuuming, pressurization, or by adding a suitable defoaming agent.
4. Dissolution time may vary depending on factors such as HPMC type, particle size, and water temperature.
In practical applications, there is no need to dissolve hot-dissolving type HPMC powder with hot water. This is because putty powder or mortar is typically found in powdered form, where HPMC is distributed among other materials through dry blending. Upon contact with water, HPMC instantly becomes viscous without caking. It’s important to note that hot-dissolving type HPMC is suitable for use only in putty powder and dry mixed mortar, while lumps may occur when used in liquid emulsions and paints. On the other hand, instant-type (surface-treated) HPMC can be extensively used in putty powder, mortar, emulsions-based adhesives, and coatings without any contraindications. However, it should be acknowledged that the water retention and stability of instant-type (surface-treated) HPMC may not be comparable to that of hot-dissolving type (non-surface-treated) HPMC. As a result, it is recommended to utilize hot-dissolving type (non-surface treated) HPMC, such as MK75P and MK100P, in dry powders such as putty powder and mortar for optimal results.
For more information, product TDS, COA, SDS, and free samples